The manufacturing sector is rapidly evolving, fueled by technological advancements and the rise of new manufacturing automation trends. With groundbreaking automation innovations in CNC machining, 3D printing, welding, and beyond, industries are finding new ways to optimize processes, enhance precision, and meet growing demand. These technologies are shaping the future of manufacturing, and their implications for the industry are profound.
CNC Machining: The Bedrock of Precision Manufacturing
CNC (computer numerical control) machining has been a cornerstone of precision manufacturing for decades, delivering unmatched accuracy and repeatability. As this technology evolves, it becomes increasingly integrated with automation and artificial intelligence. Modern CNC systems rely on the Industrial Internet of Things (IIoT) with IIoT-enabled sensors and algorithms, facilitating real-time monitoring, predictive maintenance, and process optimization. These advancements minimize downtime and maximize productivity.
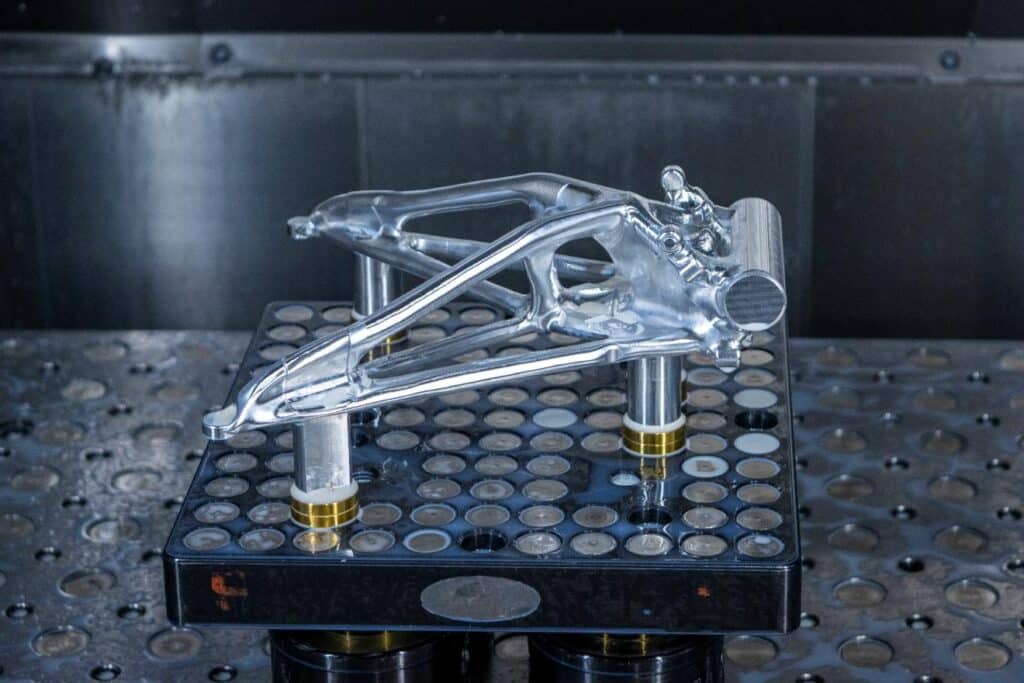
Download the Case Study!
Learn more about the unique flight hardware we produced for NASA and the ESA, generative AI applications in manufacturing, and cutting-edge advancements in CNC machining.
Another key development in CNC machining is its ability to handle advanced materials such as carbon composites, titanium, and Inconel®. The aerospace, automotive, and healthcare sectors use these materials for the high precision that CNC machining offers. Hybrid CNC machines are also gaining traction, combining additive manufacturing (3D printing) with subtractive processes. This combination enhances versatility and cuts material waste. Additionally, automation is critical in modern CNC operations, with robotic arms handling tasks like material loading and unloading, reducing human intervention and boosting efficiency.
3D Printing: The Customization Revolution
Once limited to prototyping, 3D printing—AKA additive manufacturing—has become a powerful tool for large-scale production with unparalleled flexibility and cost efficiency with the help of industrial automation and other Industry 4.0 technologies. Additive manufacturing technology enables manufacturers to produce complex geometries, lightweight structures, and intricate designs that traditional methods struggle to achieve. A significant aspect of 3D printing’s growth lies in developing advanced materials, including ceramics, composites, and biomaterials, broadening its application across industries.
The speed of 3D printing continues to improve, thanks to advancements in techniques like resin curing and laser sintering, making the technology more viable for time-sensitive manufacturing processes. Among 3D printing’s most revolutionary features is its capacity for mass customization. Sustainability is another noteworthy advantage, as 3D printing generates markedly less material waste than traditional manufacturing methods. Aerospace, automotive, and construction sectors are progressively adopting 3D printing for lightweight components, prefabricated structures, and custom designs.
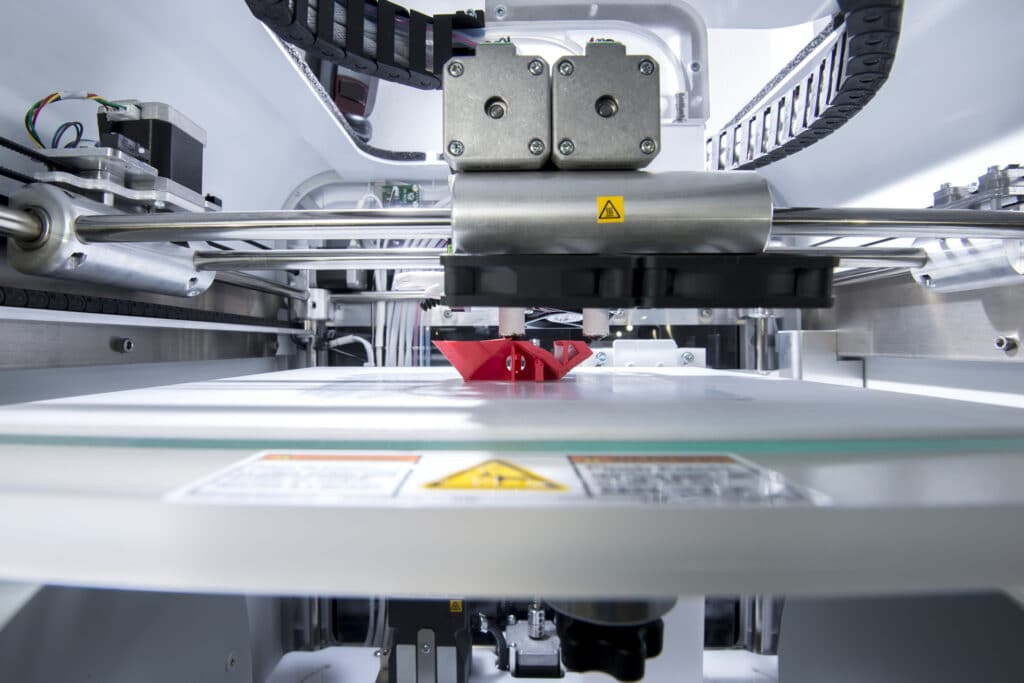
Large-Scale 3D Metal Printing: From Prototyping to Mass Production
Large-scale 3D metal printing is redefining how industries approach metal fabrication. This technology yields robust and complex metal components with minimal material waste, tackling critical challenges inherent in traditional metalworking techniques. It means cost-effective solutions for aerospace, energy, and defense industries that rely heavily on intricate metal parts.
A transformative feature of this technology is crafting large-scale metal components on-site. Manufacturers can trim costs and production delays by eliminating transporting heavy components, particularly in remote locations or challenging environments like offshore platforms. The precision and complexity achievable through metal 3D printing make it ideal for producing turbine blades, aircraft parts, and renewable energy components. As industries adopt this technology, it is poised to become a mainstream solution for high-strength, lightweight, and custom metal fabrications.
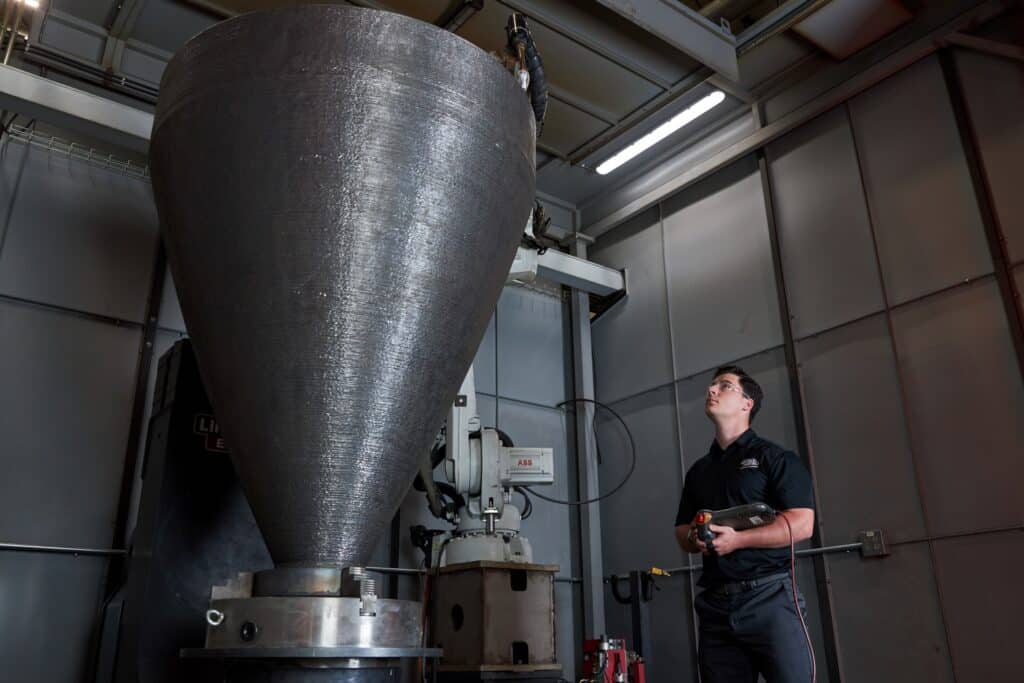
Automation and Integration: The Age of Smart Robotics
Automation has become the backbone of modern manufacturing, driving the transition to smart factories and revolutionizing how industries operate. Choosing a reliable integration partner is critical in this transformation, connecting machines, systems, and processes to form a seamless and efficient ecosystem. Robotics are a central element of automation, with robots and collaborative robots (cobots) handling repetitive tasks, heavy lifting, and precision assembly. This reduces human error, increases throughput, and enhances safety.
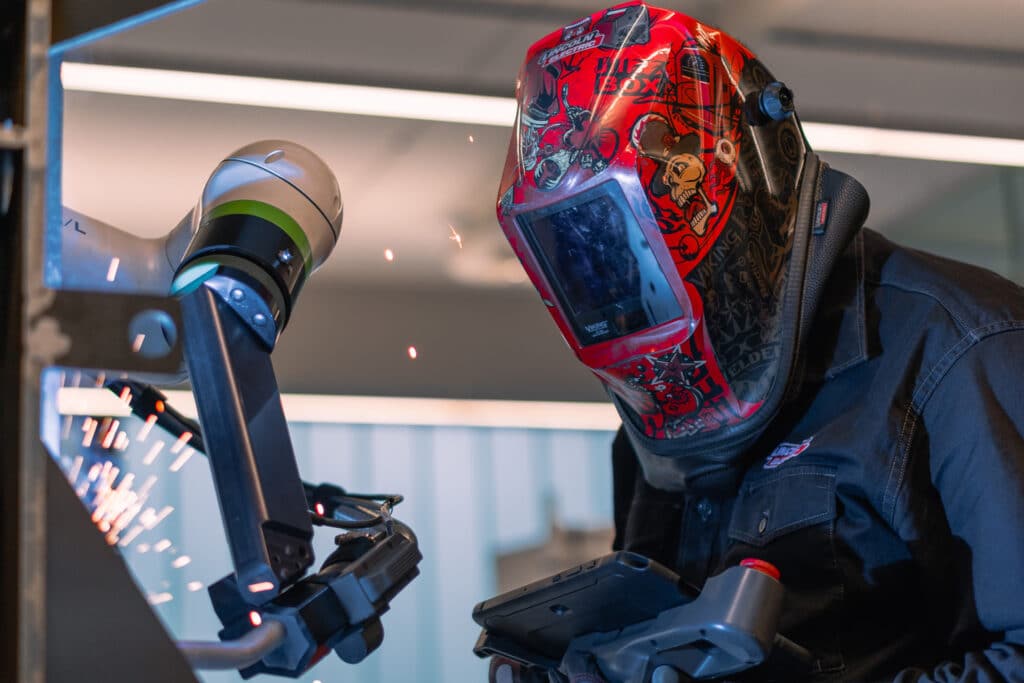
Artificial intelligence and machine learning are also reshaping manufacturing and industrial automation. AI can be used to analyze real-time production data, optimize workflows, predict equipment failures, and ensure consistent quality. IIoT-enabled devices augment connectivity by collecting and transmitting data from machines, creating a transparent and responsive production environment. Digital twins, virtual replicas of physical systems, allow manufacturers to simulate and test processes before implementing them on the factory floor, decreasing risks and improving efficiency.
The integration of automation technologies can deliver multiple benefits, including increased productivity, reduced operational costs, and greater scalability. Automated systems make it easier for manufacturers to respond to fluctuations in demand so that production lines operate optimally. Quality control is another area where automation excels, as integrated systems can detect defects and inconsistencies early in production, lowering waste and improving customer satisfaction.
Manufacturing Trends in Tandem
The future of manufacturing lies in the relationships between these technologies. CNC machining, 3D printing, and automation are not standalone solutions but interconnected tools that complement each other to build a more efficient and sustainable manufacturing ecosystem. For example, a smart factory might use CNC machines with IIoT-enabled sensors for precision machining, 3D printers for prototyping or custom components, and automated systems to streamline assembly and quality control.
This interconnected approach lets manufacturers achieve unprecedented levels of efficiency and flexibility. By leveraging the strengths of each technology, industries can address complex challenges, meet customer demands, and stay competitive in an increasingly globalized market.
Embracing the Future of Industrial Technology
The rapid evolution of manufacturing technology underscores the need for industries to adapt and innovate. Technologies like CNC machining, 3D printing, and automation are not just reshaping how products are made—they are redefining the possibilities of what manufacturing can achieve. These advancements result in improved precision, reduced costs, and enhanced sustainability, making them indispensable for the factories of tomorrow.
Manufacturers embracing these manufacturing automation trends can maintain a competitive edge while fostering greater sustainability and an efficient future. By integrating these technologies, organizations can unlock new levels of productivity and innovation, ensuring their place at the forefront of the manufacturing revolution. The future of manufacturing is here, and it is smarter, faster, and more connected than ever.