Welding and fabrication have transformed dramatically over the years. What once relied on traditional methods has now embraced innovative techniques, pushing the boundaries of what’s possible. This evolution isn’t just about technology. It’s about achieving unparalleled precision and efficiency to meet modern manufacturing demands.
Staying ahead means continually adopting new practices and tools in an industry where excellence is critical. Explore the latest welding and metal fabrication approaches and advancements that redefine standards and drive the market forward.
Welding and Fabrication Overview
Welding and fabrication are central processes in manufacturing that join and shape metal to create structures and products. The welding process involves melting and fusing two or more pieces of metal, often adding filler material. Fabrication, on the other hand, encompasses a broader range of processes, including cutting, bending, welding, brazing, and assembling metal parts to form a final product.
Together, these techniques enable creators to craft everything from intricate components to large-scale structures, playing a vital role in many industries.
Key Welding Techniques
MIG Welding (GMAW)
Among the several types of welding, metal inert gas (MIG) welding is one of the most frequently used due to its versatility and speed. This process feeds a continuous wire electrode through a welding gun while shielding the weld pool with an inert gas. MIG welding is also known as gas metal arc welding (GMAW) and is ideal for thick materials and large-scale projects, offering high deposition rates and minimal post-weld cleaning. It is particularly effective for welding metals such as aluminum, stainless steel, and other non-ferrous metals.
TIG Welding (GTAW)
Precision and control are hallmarks of TIG welding, also called gas tungsten arc welding (GTAW). In this technique, non-consumable tungsten electrodes are used along with inert gas shields to protect the weld area from contamination. TIG welding is perfect for intricate work and thin materials, producing clean, high-quality welds essential for critical applications. Various industries, such as aerospace, automotive, and piping, employ this welding process to ensure precision and integrity.
Laser Welding
Laser welding uses a high-intensity beam to join materials. This highly accurate method produces minimal distortion and a small heat-affected zone. Laser welding suits high-precision fields such as electronics, medical devices, and automotive manufacturing. Its ability to create solid and precise welds with minimal thermal stress makes it ideal for delicate and complex assemblies.
Stick Welding (SMAW)
Stick welding, often called shielded metal arc welding (SMAW), uses a flux-coated consumable electrode. It is well-suited for outdoor work and adverse conditions, as it is less sensitive to wind and other environmental factors. In construction, repair work, and heavy equipment manufacturing, stick welding is practical for welding thick materials.
Pulsed MIG and TIG Welding
Pulsed MIG (GMAW-P) and pulsed TIG (GTAW-P) welding are advanced variations of traditional MIG and TIG welding procedures. These techniques pulse the current to reduce heat input and improve control over the weld pool. Pulsed welding is particularly beneficial for thin materials and applications where heat distortion must be minimized. It enhances weld quality, reduces spatter, and allows for better control over weld penetration and bead appearance.
Other Fabrication Methods
Waterjet Cutting
With waterjet cutting, high-pressure water, often mixed with an abrasive substance, cuts through various materials with incredible accuracy. It helps cut complex shapes and materials sensitive to high temperatures, such as composite materials, glass, and metals. Waterjet cutting produces smooth, burr-free edges and does not introduce heat-affected zones, preserving the material’s structural integrity.
Plasma Cutting
Plasma cutting employs an electrically conductive gas to create a high-temperature plasma arc that melts and cuts through metals. With its speed and precision, plasma cutting is perfect for cutting both thick and thin metals like stainless steel, aluminum, and copper. Due to its efficiency and the ability to handle many different material thicknesses, plasma cutting is widely used in fabrication shops, automotive repair shops, and industrial construction companies.
Laser Cutting
Laser cutting allows for precision and minimal waste in cutting materials, including metals, plastics, and composites. It is highly accurate, fast, and capable of producing intricate designs and patterns. This fabrication process is used throughout aerospace and defense, electronics, and custom manufacturing industries, among others, where precision and detail are vital.
Press Braking
Press braking bends sheet metal into desired shapes using a press brake. This method is required for components with curved surfaces and angles, such as brackets, enclosures, and frames. Advanced press brake machinery can handle a variety of materials and thicknesses.
Roll Forming
During roll forming, a long strip of metal, typically coiled steel, is continuously bent through successive rolls until complex shapes are achieved. This fabrication process is highly efficient for producing long lengths of shaped sections, such as channels, angles, and tubes. Automobile, construction, and appliance industries rely on roll forming to produce precision parts in high volumes.
Bump Forming
Bump forming is effective in creating large-radius bends or curves in metal sheets or plates. Small, incremental bends can achieve precise contours and shapes, which would be impossible with a single bend. Bump forming is particularly useful for fabricating complex components such as composite layup molds, aircraft skins, architectural elements, and custom metalwork.
Automated Welding and Cutting
Automated welding and cutting systems represent the forefront of modern manufacturing, offering enhanced efficiency and precision. These advanced solutions overcome traditional methods’ limitations by delivering consistent, high-quality results with minimal human intervention.
Automated systems include a variety of technologies designed to streamline production processes:
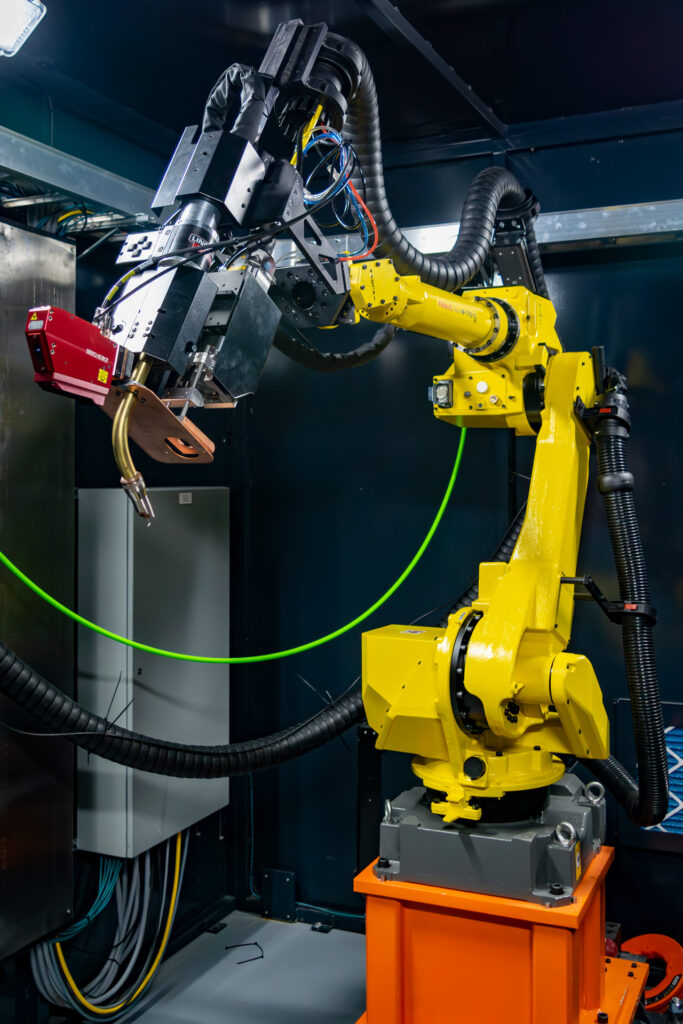
- Robotic Welding Systems: Automated machines that perform welding tasks with high accuracy and repeatability.
- Collaborative Robotic Systems: Robots that work alongside human operators to enhance productivity and safety.
- Mechanized Automation: Equipment that automates specific tasks within the welding process.
- Robotic Laser Systems: High-precision systems that use laser technology for welding and cutting applications.
- Positioners: Devices that hold and position workpieces accurately during the welding process.
- Automated Cutting Systems and Equipment: Machines that perform cutting operations precisely and efficiently.
- Robotic Grinding Systems: Automated systems for grinding and finishing metal surfaces.
- Spray and Die Casting/Foundry/Forging Systems and Equipment: Advanced equipment for specialized manufacturing processes.
These advanced systems enable manufacturers to automate processes, improve productivity, and uphold superior quality across various applications.
Commitment to Quality and Innovation
Leading companies in the welding and fabrication sector employ American Welding Society (AWS) certified welding inspectors (CWI) and certified welding supervisors (CWS) to ensure every project meets the highest standards. CWIs meticulously inspect welds for defects, verify material, and ensure adherence to precise welding procedures, and CWS professionals oversee welding operations, optimize workflow, and implement best practices. This combination of expertise and oversight guarantees that each product is precise, durable, and reliable, reflecting a commitment to continuous improvement and integrating the latest welding technology.
Metal fabrication and welding techniques must keep up with the changing manufacturing landscape. Baker Industries leads these advancements and offers unmatched expertise and innovation. From manual welding and cutting to advanced methods like automated welding and CNC cutting, our comprehensive capabilities deliver superior quality and precision for every welding project.
Discover why Baker Industries is the trusted partner for businesses seeking excellence and innovation in welding and fabrication. Contact us today for expert guidance and to discuss your particular needs.