Aerospace CNC machining has revolutionized the manufacturing landscape of the aviation, defense, and space industries. As the demand for precision, efficiency, and innovation continues to evolve, advanced CNC machining methods have emerged as essential in producing complex aerospace components. These cutting-edge procedures have tremendous implications for the future of aerospace manufacturing.
Understanding Aerospace CNC Machining
CNC (computer numerical control) machining entails using computer software to control machine tools for manufacturing parts with high precision. Safety and reliability are fundamental in the aerospace sector, and CNC machining is indispensable for producing parts that meet strict industry standards.
Critical Applications of Aerospace CNC Machining
The aerospace industry uses CNC machining for various applications:
- Structural components for airframe structures
- Engine parts such as turbine blades, casings, and fuel systems
- Interior components comprising lightweight, durable parts for cabin interiors
- Landing gear systems relying on precision parts
- Tooling and equipment used to manufacture parts
- Ground support equipment to service aircraft between flights
These applications epitomize the importance of CNC machining in achieving the rigorous performance standards required in aerospace manufacturing.
Advanced CNC Machining Techniques
5-Axis CNC Machining
5-axis CNC machining is one of the most advanced methods in the aerospace industry. Unlike more-traditional 3-axis machining, which can only move along the X, Y, and Z axes, 5-axis machines can rotate on two additional axes. This capability means manufacturers can produce more complex geometries and intricate designs in a single setup, significantly reducing production time and improving accuracy.
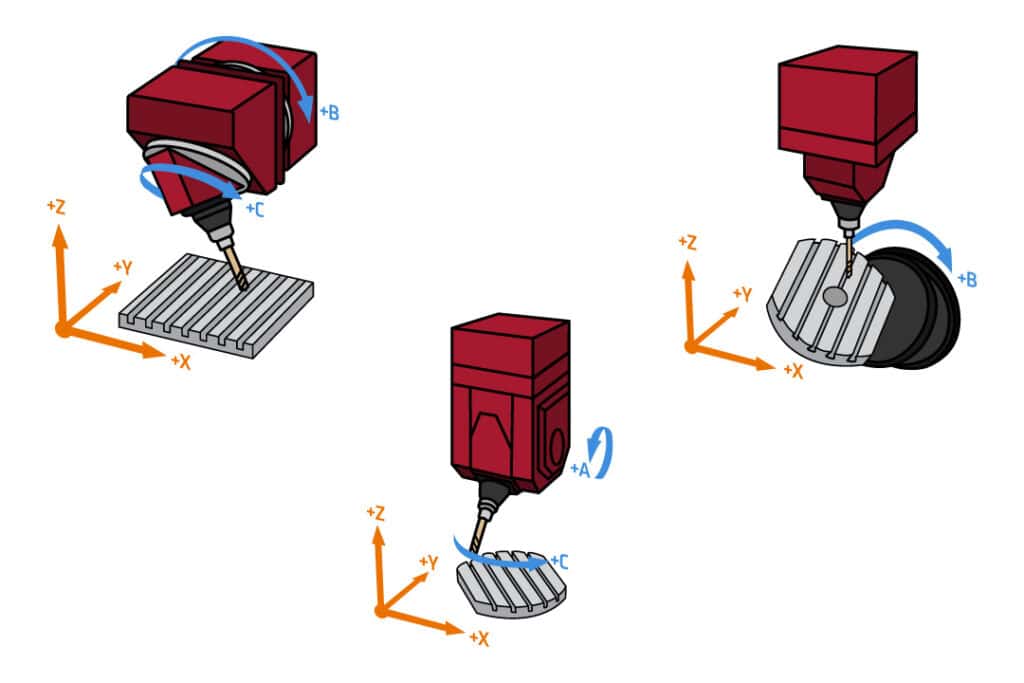
Advantages of 5-Axis Machining
- Enhanced precision reduces errors from repositioning workpieces.
- Complex part production can create intricate shapes typically impossible with 3-axis machines.
- Better tooling angles and reduced wear result in a superior surface finish.
Multi-Tasking Machines (MTM)
Multi-tasking machines merge multiple machining processes into one operation. For example, a machine may perform milling, turning, and drilling within the same setup. This integration reduces the need for multiple machines and minimizes handling, which is invaluable in aerospace, where precision is non-negotiable.
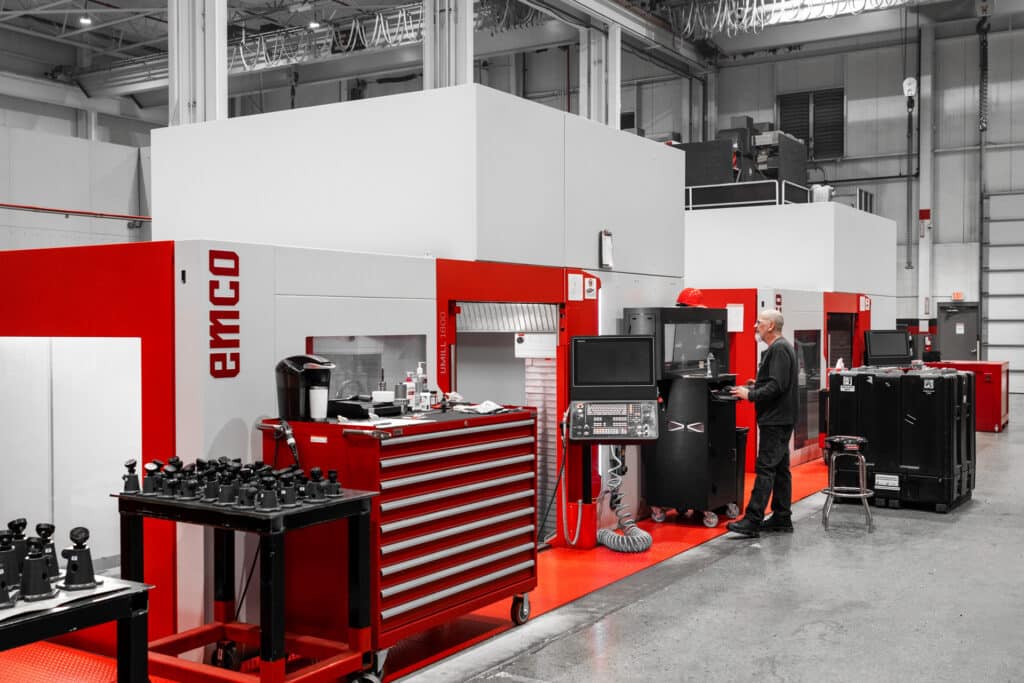
Benefits of Multi-Tasking Machines
- Increased Efficiency: Streamlined processes lead to faster production cycles.
- Less Downtime: Fewer setups and/or machine changes translate to more operational time.
- Higher Accuracy: Maintaining parts in a single setup minimizes the risk of misalignment.
Additive Manufacturing Integration
Integrating additive manufacturing (AM) with CNC machining techniques is a game-changer in aerospace production. 3D printing creates complex geometries that traditional manufacturing processes cannot achieve. Manufacturers can produce lightweight, high-strength parts with optimized material usage and complex features by combining AM with CNC processes.
Advantages of Additive Manufacturing
- Reduced Waste: Use only the material required for production.
- Customizability: Create tailored components for specific applications with complex features and geometries.
- Accelerated Go-to-Market: Rapid prototyping accelerates go-to-market timelines by allowing for quick design iterations.
High-Speed Machining (HSM)
High-speed machining focuses on increasing the speed of the cutting process, resulting in faster production rates without sacrificing the quality of the final product. This method is particularly beneficial for machining aluminum and composite materials, which are common in aerospace applications.
Key Benefits of High-Speed Machining
- Reduced cycle times lead to increased productivity.
- Improved tool life occurs because there’s less wear and tear.
- Better surface finish
Material Considerations in Aerospace CNC Machining
Choosing materials in aerospace CNC machining is critical, as they must withstand extreme conditions while maintaining structural integrity, reliability, and safety. Commonly used materials are highlighted below:
- Aluminum alloys are lightweight and corrosion-resistant, making them ideal for airframe components.
- Titanium alloys are known for their high strength-to-weight ratio and are commonly used in engine parts.
- Inconel® is known for its ability to withstand extremely high temperatures, making it another popular choice for engine parts.
- Invar® has a low coefficient of thermal expansion (CTE), meaning that it expands very little when heated, and is a popular choice for layup molds used for composite part fabrication and similar applications.
- Composite materials have lightweight properties and are resistant to fatigue.
These materials pose unique challenges in machining, requiring advanced techniques and tooling to achieve optimal results.
The Role of Automation and Industry 4.0
Automation and the principles of Industry 4.0 are increasingly being adopted in aerospace CNC machining. Smart factories equipped with Industrial Internet of Things (IIoT) technology allow for automation and real-time monitoring and data analysis, leading to improved decision-making and efficiency.
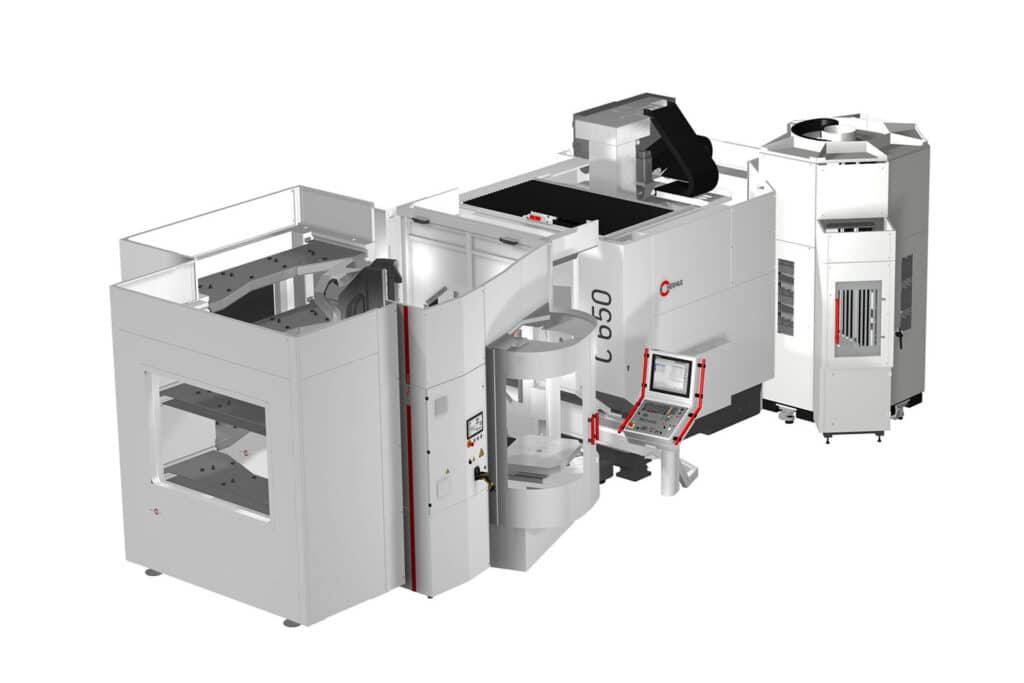
Benefits of Automation
- Increased Productivity: Automation reduces manual intervention and errors and allows for lights-out production.
- Predictive Maintenance: IioT sensors and other technology monitor equipment and predict maintenance needs and failures, minimizing downtime.
- Enhanced Quality Control: Automation ensures consistent quality by reducing the risk of human error and providing real-time data analysis capabilities.
- Improved Workplace Safety: Automation minimizes human intervention, reducing the risk of injuries during machine operation, lifting heavy materials, etc.
Future Trends in Aerospace CNC Machining
The future of aerospace CNC machining is promising, with several trends expected to shape the industry in the coming years. Some key trends are explained here:
Increased Focus on Sustainability
As the aerospace industry seeks to reduce its environmental impact, manufacturers can optimize CNC machining and auxiliary processes for sustainability using eco-friendly materials, energy-efficient machines, and waste-reduction strategies.
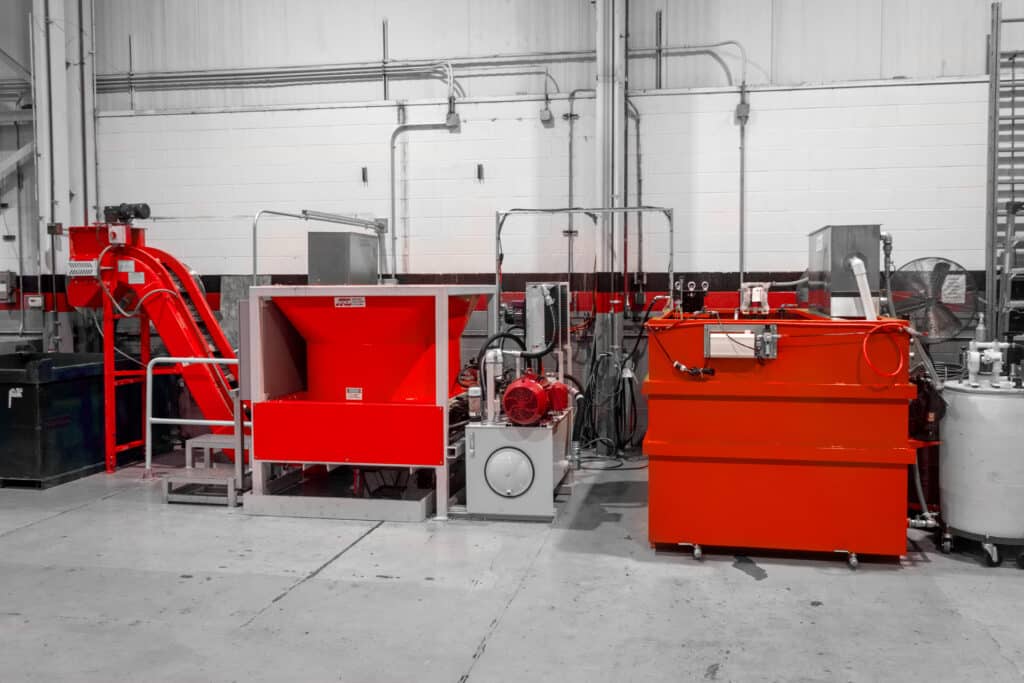
Advanced Software Solutions
The evolution of CAD/CAM software makes it easier for manufacturers to design complex parts and optimize machining processes. Enhanced features like simulation, toolpath planning improvements, and real-time feedback are expected to become standard.
Greater Adoption of Artificial Intelligence (AI)
AI is set to play a significant role in aerospace CNC machining, from predictive analytics to augmenting machining processes. By harnessing the power of AI, manufacturers can improve efficiency and reduce costs while maintaining high-quality standards.
Embrace New Technologies or Risk Being Left Behind
Advanced aerospace CNC machining techniques are transforming the manufacturing processes within the aviation, defense, and space industries. As the demand for precision and efficiency grows, embracing technologies such as 5-axis machining, multi-tasking machines, and additive manufacturing will be pivotal to staying competitive. Additionally, integrating automation and AI will further augment these processes, paving the way for a more sustainable and innovative future in aerospace manufacturing.
With these methods continuously evolving, manufacturers must remain vigilant and adaptable, ensuring they are prepared to meet the challenges and opportunities that lie ahead in aerospace CNC machining.