By 3D printing the mill fixture using ABS thermoplastic material instead of machining it from aluminum, Baker was able to reduce the tool’s weight by 70 percent, which served to protect the parts being trimmed and provide a safer solution for employees handling the tool.
In addition to providing significant weight reduction, 3D printing the tool enabled some time savings in production. The team was able to print the tool in approximately fifty hours, saving the customer a week of lead time that would have normally been required to traditionally machine this tool.
Due to the high precision tolerances and the complexity required for this application, the cost was not significantly changed, but rather comparable.
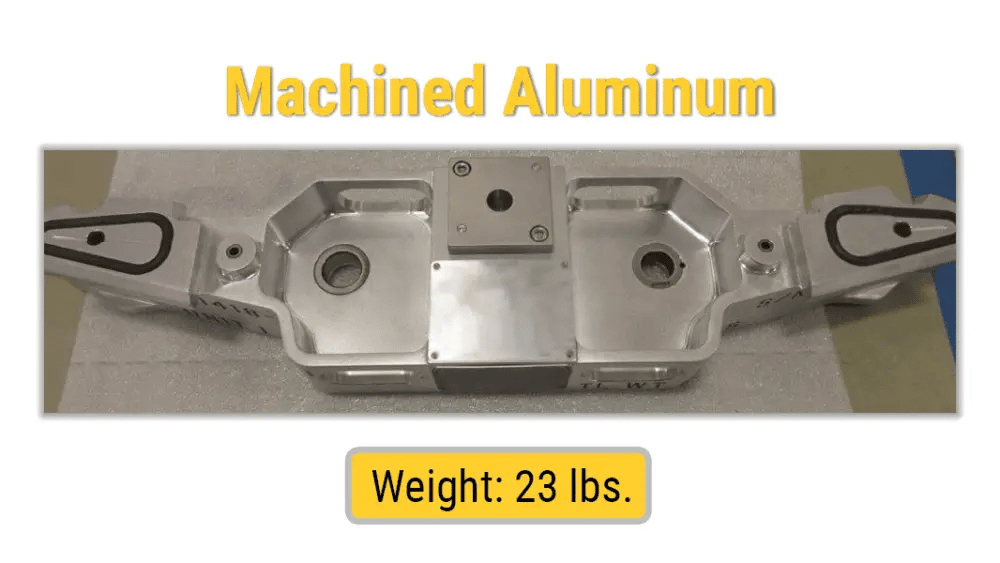