Automation integration services have emerged as a game-changing solution for manufacturing companies to optimize production processes. From reducing operational costs to improving product quality, automation technologies can revolutionize manufacturing facilities’ operations. Here are five transformative ways automation services can enhance your production line.
Automation Integration: Increased Production Efficiency and Output
One of the most considerable advantages of implementing automation integration services is the dramatic boost in production efficiency. Automated systems can operate continuously without fatigue, maintaining consistent production rates throughout multiple shifts. Unlike human operators, these systems don’t require breaks or experience productivity dips and can work 24/7.
Modern automation solutions use advanced robotics and programmable logic controllers (PLCs) to perform repetitive tasks with unprecedented precision. Automation raises daily production output while supporting higher quality standards. Operating 24/7 with minimal downtime translates directly into increased production capacity and improved return on investment.
Quality Control and Consistency
Quality inconsistency is costly for manufacturers and leads to waste and damaged reputation. Automated quality control systems like the Zeman™ ENSPECTOR™excel at preserving strict quality control standards through sophisticated inspection systems, reduced room for human error, and precise execution of manufacturing processes.
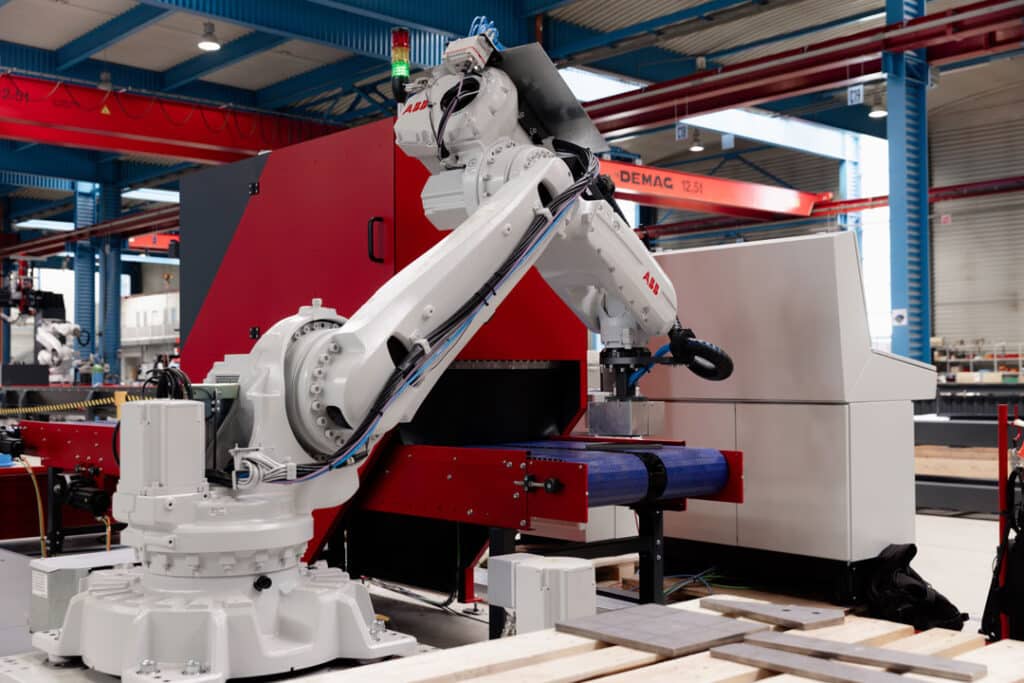
Machine vision systems can inspect hundreds of products per minute with accuracy levels that surpass human capabilities. These systems can detect microscopic defects, verify proper assembly, and ensure correct packaging—all in real time. Additionally, automated production processes eliminate human error in repetitive tasks, ensuring consistent product quality across production runs.
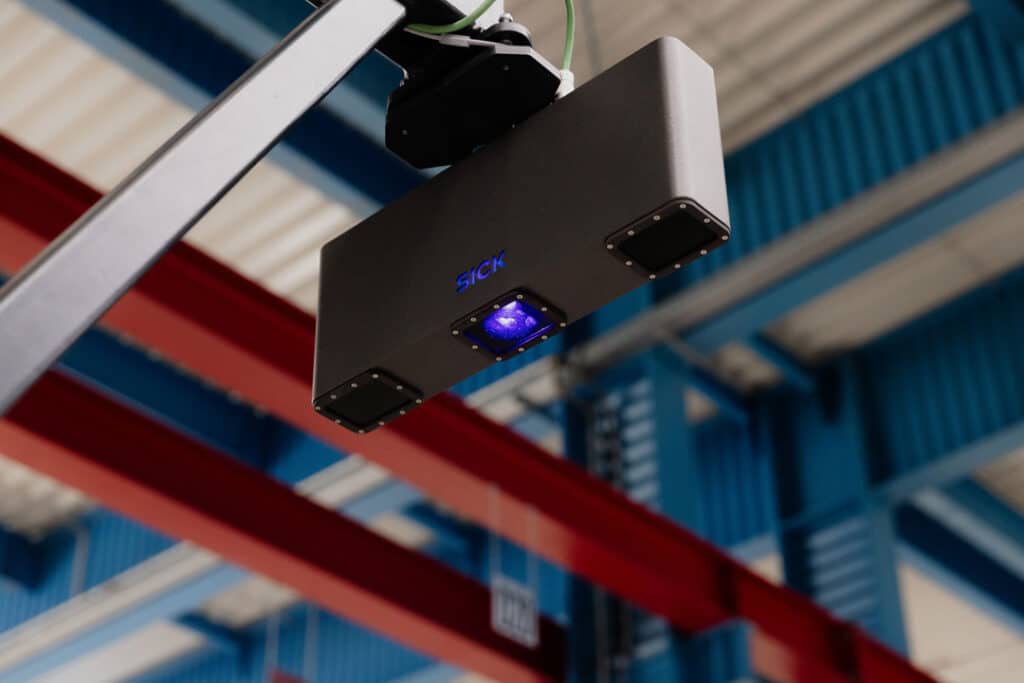
The results are compelling: manufacturers implementing automated quality control systems see dramatic reductions in defect rates, saving costs and improving customer satisfaction.
Data-Driven Decision-Making
Modern automation systems have advanced sensors and monitoring capabilities that generate vast amounts of valuable production data. This information provides unprecedented visibility into your manufacturing processes, enabling data-driven decision-making and continuous improvement.
Key benefits are highlighted below:
- Real-time monitoring of production metrics
- Predictive maintenance scheduling
- Resource utilization tracking
- Performance bottleneck identification
- Energy consumption optimization
Companies can identify inefficiencies and decide production scheduling and maintenance activities by analyzing this data. Preventing equipment failures before they occur can significantly reduce costly downtime and maintenance expenses.
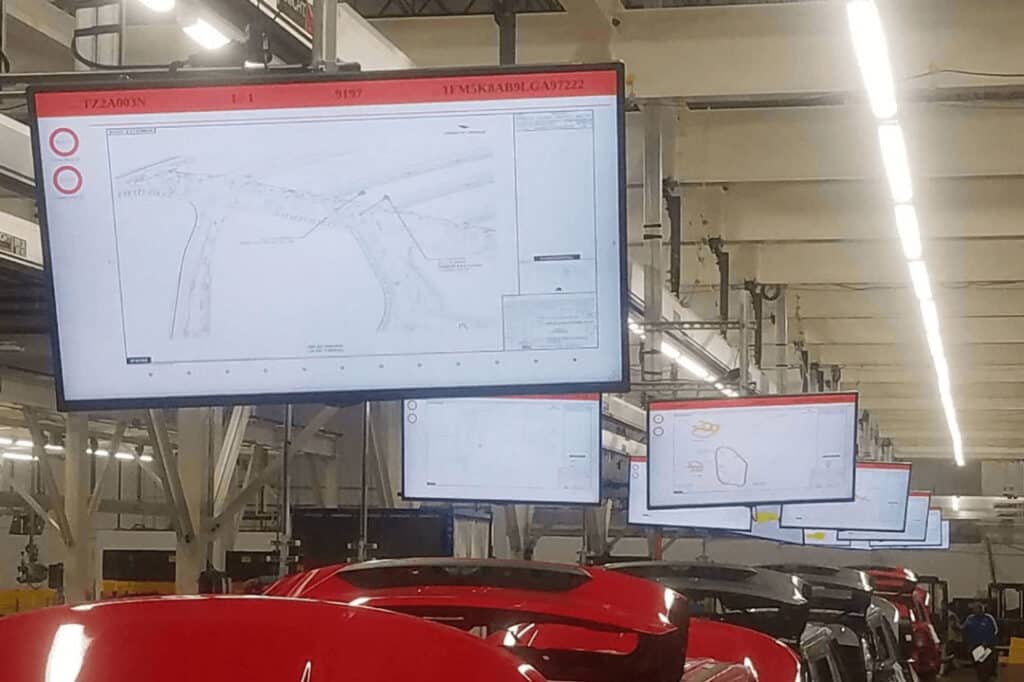
Heightened Workplace Safety
Workplace safety remains a top priority for manufacturers, and automation is paramount in creating safer working environments. Automated systems can handle dangerous tasks that would otherwise put human workers at risk, such as:
- Working with extreme temperatures
- Handling toxic materials
- Operating in confined spaces
- Performing repetitive motions that could lead to injury
- Managing heavy-lifting operations

Modern collaborative robots (cobots) have advanced safety features that work with human operators while maintaining strict safety protocols. In some facilities, automation in hazardous areas has been shown to reduce workplace accidents by up to 72%.
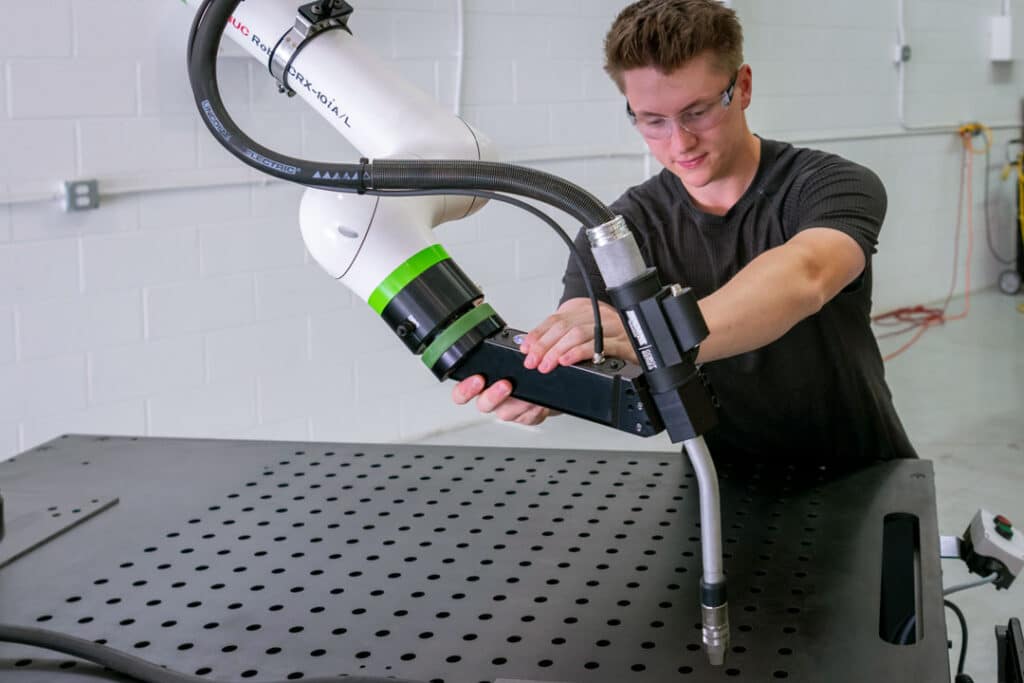
Greater Flexibility and Scalability
Contrary to popular belief, automation solutions offer remarkable flexibility and scalability. Today’s automated systems can be quickly reprogrammed to accommodate different products, variations, or production requirements, allowing manufacturers to adapt to changing market demands without significant downtime or retooling costs.
Other ways automation systems benefit manufacturers include:
- Easily modify production processes
- Scale operations based on demand
- Implement changes without disrupting entire production lines
- Add new capabilities incrementally
- Respond quickly to market trends and customer requirements
This flexibility is invaluable in industries with frequent product changes or seasonal variations in demand. Manufacturers can quickly adjust their production parameters without extensive retraining or restructuring of their workforce.
Integrating Automation Successfully
While the benefits of automation are clear, successful implementation requires careful planning and consideration. Organizations should follow these steps:
- Conduct thorough assessments of current processes
- Identify specific areas where automation will provide the greatest return on investment
- Develop a phased implementation strategy
- Invest in proper training for existing staff
- Partner with experienced automation service providers like Lincoln Electric Automation
Although the initial investment in automation technology may seem substantial, the long-term benefits—including higher productivity, improved quality, enhanced safety, and reduced operational costs—typically result in a positive return on investment over time.
Embracing the Automation Revolution
Transforming production lines through automation integration services represents a notable opportunity for manufacturers to improve their operations and maintain competitiveness in an increasingly challenging market. By carefully considering and implementing these automation solutions, manufacturers can achieve higher productivity, better quality control, improved safety, and greater operational flexibility.
As technology advances and automation solutions become more sophisticated and accessible, the question for many manufacturers is no longer whether to automate but how to implement automation most effectively to achieve their specific production goals and remain competitive in their industry.